Industrial Air conditioning with Temperature and RH control
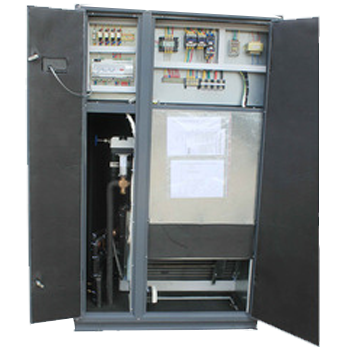
Air conditioning is the mechanical replacement of heat with cooled air. The indoor air quality – related to industrial Air conditioning is major concern to meet process related, product related activities. Basic design is as per ACGIH standards & to meet good manufacturing practices. Air conditioning systems are required generally in industry
To maintain indoor dry bulb temperature & percentage of relative humidity under controlled levels to meet critical process and product requirement.
To create comfort zone by maintaining indoor air quality.
A deadly enemy of most electronic equipment and personal productivity is heat. Machinery used to produce critical equipment or to do some precision work requires constant cooling to function properly. In a commercial facility / production area, personal comfort level is very much important by maintaining good indoor air quality to maintain health of personal in turn to increase the productivity.
Air conditioning system Design Parameters are:
Manufacturing process
Required indoor conditions
Outdoor ambient conditions
Connected equipment load
Heat emissions
No. of people presence inside the environment
Sunlight exposed surface area of enclosure
Lighting load
Cleanliness requirements
Heat emissions
Regulations
The applications of these systems are as under:
Pharmaceutical / Bulk Drug industries
Photo / electronics industries
Food Industries
Biotechnology, bioscience laboratories
Clean rooms (engineering / biotech / pharma products / Assembly of precision components)
Mechanical Ventilation Systems
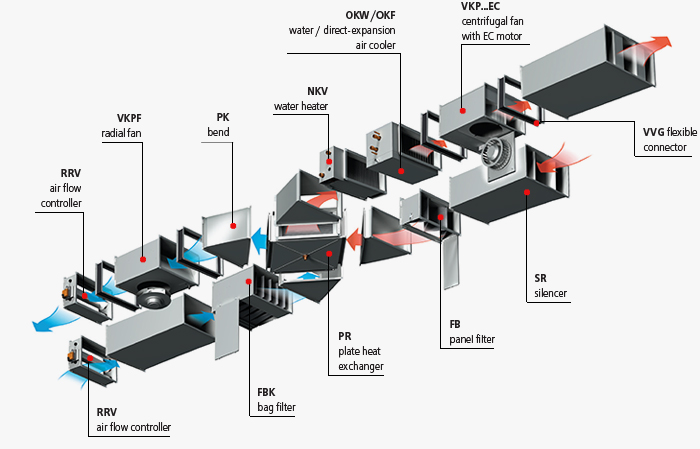
Large industrial areas are not economical to provide temperature controlled air conditioning system. Alternatively to enhance the indoor operators comfort level a filtered fresh air ventilation system is most suitable with adequate number of air changes as per ventilation standards & WHO standards. Generally, mechanical ventilation system is required,
- To provide necessary comfort level conditions for maintaining the efficiency, health and safety of the workers
- To control hazardous concentrations of toxic materials in the indoor air
- To maintain cleanliness level of indoor air
- To maintain adequate oxygen supply in the work area
- To remove any undesirable odors from a given area.
- Ventilation Design Parameters are
- Manufacturing process
- Exhaust air system & local extraction
- Cleanliness requirements
- Ambient air conditions
- Heat emissions
- Contaminant emissions
- Regulations
Mechanical ventilation system comprises of following
- Air inlet section
- Filters
- Heating and/or cooling equipment
- Blowers / Air Handing units
- Ducts
- Register/grills for distributing the air within the work space
Some process requires a dust proof environment – to ensure this the areas are pressurized with filter supply air which maintains positive pressure inside process areas their by outside air contamination can be totally avoided. Most of food manufacturing & packaging industries demands pressurization systems to make their product more hygienic.
The mechanical ventilation systems are designed for different industries. Followings are the type of industries uses mechanical system.
- Pharmaceutical
- Food industries
- Packaging industries
- Bio-technology
- Chemical industries
- Plastic / Rubber molding
- Steel plants
- Electronic Industries
Evaporative Cooling system
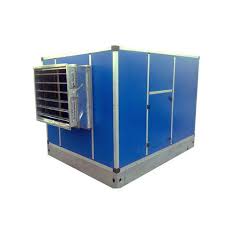
Evaporative cooling systems have added advantage in achieving higher comfort level in manufacturing & general engineering industries. Ventilation supply air systems draws the outside air & filter it to the required micron level & distribute air to occupied areas to meet comfort. In evaporative cooling system, the same fresh air system is equipped with a water circulated cooling pad & the filtered dry air at ambient temperature is allowed to pass through cooling pad, their by the dry bulb temperature of air it will brought down and cooled air will be distributed to the occupied areas. Which make more comfort if the occupied area. This is an adiabatic cooling process where large occupied areas to be brought under comfort level.
Evaporative cooling systems have added advantage in achieving higher comfort level in manufacturing & general engineering industries. Ventilation supply air systems draws the outside air & filter it to the required micron level & distribute air to occupied areas to meet comfort. In evaporative cooling system, the same fresh air system is equipped with a water circulated cooling pad & the filtered dry air at ambient temperature is allowed to pass through cooling pad, their by the dry bulb temperature of air it will brought down and cooled air will be distributed to the occupied areas. Which make more comfort if the occupied area. This is an adiabatic cooling process where large occupied areas to be brought under comfort level.
In case if it use a chilled water spray in the cooling pad in place of normal water the room temperature will be still better & close to air conditioning comfort. This application has a main disadvantage is the relative humidity level will be high (over 70%) which place an important role & can affect the manufacturing process & products where the humidity levels are the criteria.
Evaporative cooling system comprises of following
- Air inlet section
- Filters
- Water circulated cooling pad
- Re circulation water pump with internal water sump
- Blowers / Air Handing units
- Ducts
- Register/grills for distributing the air within the work space
Humidification Plant
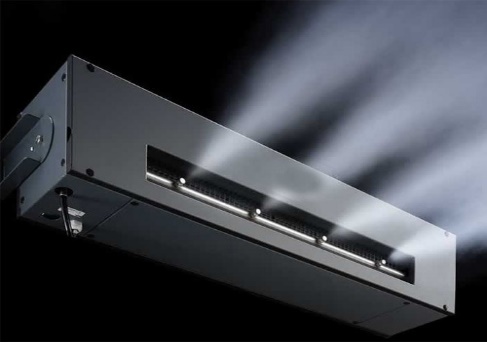
This is a process requirement design where humidity levels requirement is more than 60 to 70% simultaneously enhances the comfort level due to adiabatic cooling process. Indoor Air Quality solutions mushroomed in the Industries as the process demands controlled humidity level and people become more aware of health related issues. The ASHRAE standard range for optimum indoor relative humidity is between 40-60% year round. Controlling indoor relative humidity is important to health because too little humidity can create microscopic cracks in a person’s nasal membrane, leaving the body more vulnerable to infections from bacteria and viruses. Conversely, too much humidity creates ideal breeding conditions for mold, mildew and dust mites; from which the waste products are among the most troublesome triggers of asthma and allergies. The outside air is filtered & allows passing through a water spray zone in the Air Handling Unit. The air leaving the water spray zone will have more moisture & this air will be distributed to the manufacturing / process area to meet their process requirement. The following industries generally needs humidification plant
- Tobacco process
- Textile process
- Painting
- Wood working
- Hospital
- Pharmaceutical
- Food processing
- Printing
- Steel rolling mill
Dust Proofing / Pressurization Systems
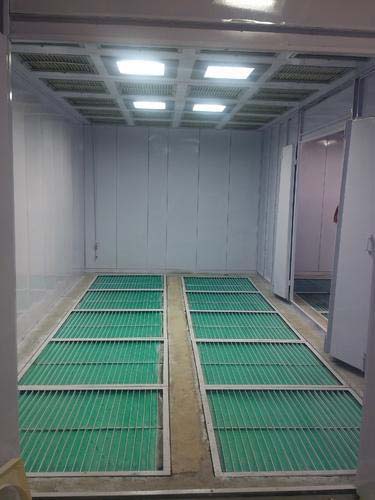
Dust Proofing System is requirement of certain process / activities such as assembly of precision components, packing of precision products, painting process, electronic components assembly. Dust proofing environment requirement arises
To keep the environment as dust free zone to suit to the process / activity To create comfort level and more Hygienic environment for the occupants in a specified area, if the outside area is having pollutant like dust or any hazardous chemica